When a fish production factory in Russia needed to ensure the latest catch could be frozen quickly ready for export to diners around the world, they looked no further than Fairford Electronics and their proven soft starter technology.
Russia, which is the fourth largest producer of frozen fish in the world, has an expanding network of factories in the St Petersburg area to service growing global demand. A key requirement is ensuring refrigeration units retain constant temperatures so none of the valuable products are rendered unfit for consumption due to any fluctuations.
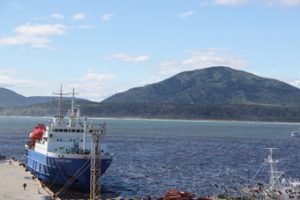
The waterside setting of the fish production factory in St Petersburg.
Cold Trade Ltd, also based in Russia, installed a plant for fish production at one of these factories but needed to overcome the challenge of having the lowest starting current possible on the refrigeration units.
This low starting current is essential because refrigeration units have high starting currents which can cause damage to components as well as increasing maintenance downtime. If caviar is being produced in the factory at the time, then this downtime could put the sale of millions of dollars of fish at stake.
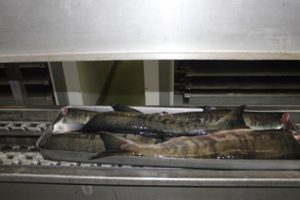
Fish being prepared to be frozen at the factory.
Denis Bobin, a controls engineer with Cold Trade, worked with Fairford to specify a suitable soft starter for this application.
He says: “Russia is expected to produce five million tonnes of seafood annually by 2018 and, with the proportion of frozen fish rising to a record high of 57% in 2014, such factories need to be able to ensure their refrigeration plants will not break down due to any power surges.
“Soft starters will ensure that the fixed speed motor on the refrigeration units will run as efficiently as possible and also prolong their life. This is particularly important because the units are in use around the clock to ensure all fish catches are frozen quickly and have the best possible taste before reaching dining tables across the world,” he added.
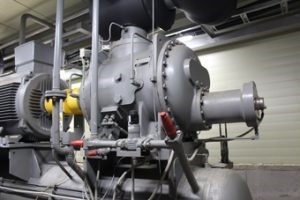
One of the 250kW cooling compressors.
Fairford supplied two 280kW synergy units for use on the 250KW cooling compressors with semi-conductor fuses.
Steve Atkey, technical sales engineer at Fairford, explains: “Using Fairford’s 3.5ins touch screen, automatic application set-up and automatic features, the two SGY-401 units were installed and commissioned at this factory in a matter of minutes.
“The automatic features modify the start and stop ramps to ensure that the optimum settings are always selected to give the smoothest possible start (or stop).
“Denis chose to work with us on this particular application because of past experience of our products and a returning customer is always to be welcomed.
“He also cited our technical support, good delivery times and ease of set-up and use as factors in choosing us which again I am delighted with as customer service is key to ensuring we can keep building on our global success,” he added.
Find out more about synergy here.